In an interview done by Kristina Šorić, Ph.D., Professor at Rochester Institute of Technology Croatia, Ivan Gadže, the CEO of Tokić, analyzed Tokić’s business, the challenges the company has faced in recent months and the positive outcomes the regional leader in car parts sale encountered.
Together with franchise partners, Tokić Ltd is the largest retail chain of auto parts in Croatia. It is an authorized importer and distributor of over 230 of the world’s most famous manufacturers of parts for all types of cars and light trucks, as well as scooters, motorcycles, trucks and buses. The supply chain structure of this company is very complex and includes a strong international component.
1.What is the activity of the Tokić company?
Together with its franchise partners, Tokić is the biggest sales chain of the car parts in Croatia and authorized importer and distributor for over 230 of the world’s leading producers of parts for all types of personal and cargo vehicles, as well as scooters, motorcycles, trucks and buses. We are a leading Croatian company, and in these 30 years of business, the company has grown from a family business into a regional leader and a leading Croatian company dedicated to innovative technologies in the car parts industry. Our logistics and distribution center in Sesvete is on the same level as the leading European companies in the car industry.
2. What are the members of your supply chain (suppliers, transportation, warehousing/production, distribution) and how has it developed since its inception until today?
Currently, our supply chain includes all of the above: suppliers, transportation, storage and further distribution of goods, both domestically and abroad.
In addition to more than 600 people, I would like to list a few dozen automated and robotic processes that are today an indispensable link in our logistics chain. It is clear that in these three decades, the retail sector has transformed from classic counter sales to full customer service, from education and recognition of its needs to delivery to the doorstep. This also created the need for a number of new jobs and entire departments. As we are also a supplier, distributor and seller of car parts, we have recognized data management as the key to further development. Today, the procurement department plays an important role in the entire supply chain, in which we have successfully automated a part of the procurement, as well as the Tokić Stock team, which deals with inventory management and their optimal availability. Also, there is the Tokić Replenishment team which is in charge of inventory management and supply of our retail outlets with goods. We also pay a lot of attention to analytics, which gives us numerous answers and helps us make business decisions. In the previous year, we also upgraded the warehouse management system (WMS), which helps us to optimally manage the warehouse business. As a company focused on new and developing technologies, we are constantly investing in the development of artificial intelligence and data science, which already contributes to better and more efficient inventory management, as well as the entire supply chain. I would also like to point out that Tokić today has a large number of its own delivery vehicles, which is also an important link in the entire supply chain, and in this way, we have optimized transport to the maximum.
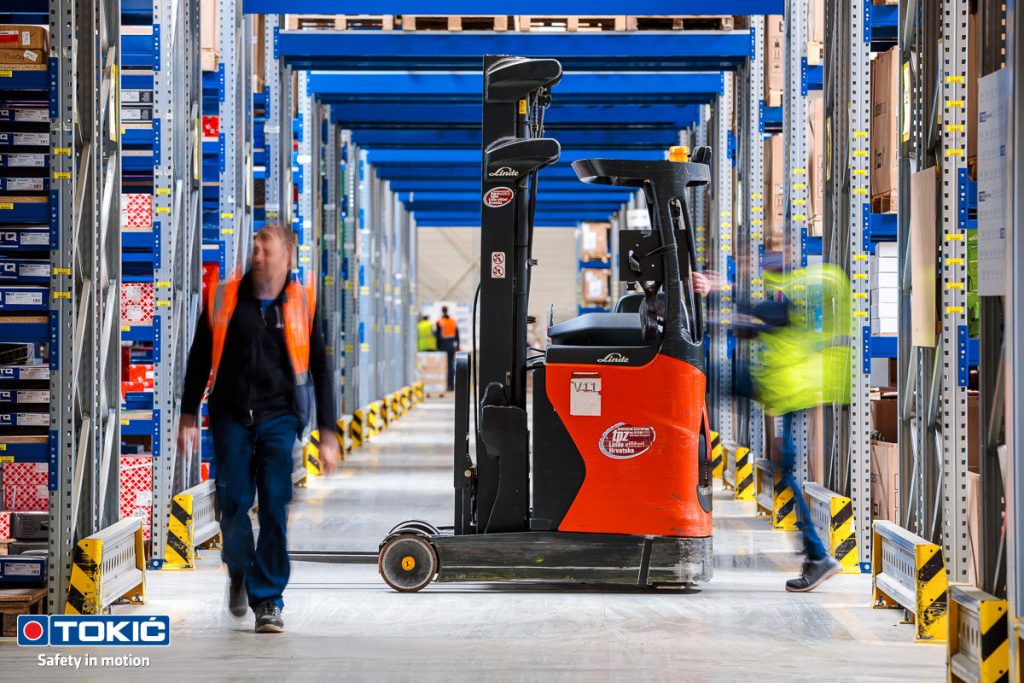
3. What are the main strategies you implement in balancing effectiveness and efficiency (delivering high quality while optimizing costs)?
One of the main strategies is primarily to develop good business relationships with suppliers. We also strive to optimize transport costs as much as possible, so we try to use our own delivery vehicles as much as possible, thus ensuring a high standard of delivery to our customers. Such a practice has resulted in the delivery of high-quality products at the lowest possible price, but also at the lowest possible cost. It is important to mention that we use the Kaizen methodology in our business, which contributes to the removal of all unnecessary steps within the process that do not bring us added value. For this purpose, we have formed a special team that deals with the implementation of Kaizen, ie lean methodology in all aspects of the business. It is important to mention that we have introduced robotics in the business – a specially programmed robot performs slow, physically demanding, automatic and repetitive tasks instead of employees, which gives us space to allow employees to work on creative and smart tasks.
4. To what extent have you implemented supply chain values such as integration, coherence, communication, transparency and mutual trust?
I can say that we have now implemented these values more than ever. We try to communicate with our suppliers and customers on a daily basis, to speak transparently and openly about the situation we are in and about all the problems. We also believe that it is very important to stick to the agreement, all in order to preserve mutual trust. Since the beginning of the crisis, we have had good and open communication with suppliers regarding changes in payment terms and reduced business activity. This is a period in which we have learned a lot about ourselves, but also about others and we believe that this is a situation that will give us answers to who are the partners with whom we want to maintain good business relationships in the future. We are extremely grateful to our suppliers who have shown maximum professionalism in these difficult times but have retained one human element in all this and show solidarity.
5. What were the first moves you took when the corona crisis broke out?
One of the first steps was the establishment of a crisis headquarters consisting of management and directors of various sectors, which on a daily basis monitor changes that occur, adapt the business to new circumstances and assist the Management Board in making decisions. I must say that this is a situation that Tokić, like most companies, could not prepare for or anticipate. However, problems need to be faced, so from day one we tackled all the problems and set out to solve them.
The first goal of the crisis headquarters was to ensure the health of our employees and their families and all our partners, customers and suppliers. In accordance with the instructions of the national headquarters, we adapted the business to the new circumstances. A large number of employees worked from home, and for those whose nature of work does not allow them to work from home, they were provided with all the conditions for the protection of health and safety at work.
Of course, in a situation such as the corona crisis, it is difficult to plan anything, but we have given and still do our best to manage this crisis as well and responsibly as possible. The management is aware that this is a period of quick decisions that can change from day to day and that there will certainly be wrong decisions, but we believe that the most important thing is not to give up and mature, from a broad perspective to look at all problems and try to solve them as efficiently as possible. We communicated all decisions very openly and clearly both within the company and to external partners. The value of transparency is something we live deeply in and it has proven to be very important in these times.
We actively followed all the decisions of the government whose activities and decisions helped companies to overcome this crisis. A very important element of these decisions was liquidity management. We have thoroughly analyzed all the measures and selected the ones that best suit our needs. We also actively participated in the initiatives of interest associations in order to show solidarity with other entrepreneurs.
As a forward-looking company, one of the first steps in the very early phase of the crisis was the establishment of a post-crisis headquarters, which is a combination of experienced managers and young and promising employees tasked with working out different scenarios for what will happen to the company, how this crisis will affect business development in the future and what strategic moves we will take. The main goal of the post-crisis headquarters was to clearly describe the new normal.
Throughout the period, communication with all partners, suppliers and customers continued on a daily basis, including small customers who also had a demand for our products. Through the contact center and webshop and in accordance with the measures in force, we offered citizens delivery or collection of goods.
6. What was/is the most complicated thing for you in that?
At the moment when the Croatian Headquarters of Civil Protection passed the decision by which we had to close all our retail outlets, our income dropped drastically and we realized that we had to take all measures to preserve liquidity and that was our main priority. Financial plans are made from day to day depending on inflows and outflows, we have decided to minimize costs that are not necessary at the moment, negotiate with suppliers, agree on longer payment deadlines and/or installments and rely on our own workforce. In order to show solidarity with our suppliers and everyone who came out to meet us, we decided to temporarily reduce the value of the coefficient for calculating the salary so that we could all bear the burden of this crisis in some way. It was not an easy decision for us, but we stand behind it and believe that it was the right one because our main focus was to preserve jobs.
On this occasion, I would like to thank all the employees who mostly reacted positively to this decision and gave the management maximum trust and support. The incredible human and business solidarity of all employees is something that will be deeply etched in our consciousness. This was especially felt at the moment when Zagreb was shaken by a strong earthquake. The entire company gave strong support to all colleagues whose homes were damaged in the quake.
The financial conditions of our employees are significantly above the average salary in Croatia and in our industry. Our basic goal is to return the level of wages to the pre-crisis level as soon as possible and make efforts to make wages even better.
7. What are the negative consequences of this situation on your supply chain?
I can say that Tokić had very good supplies status at the beginning of this crisis, so we didn’t have any problems with the availability of products for our customers. We significantly concentrated on existing inventories and their management, in which our supplies team played a major role.
In a short period of time, we had limited access to goods from the market that were more severely affected by the crisis and we could not deliver to some countries. However, it is important to say that it didn’t last long.
8. And the positive ones?
The positive side is certainly that we had to adapt quickly to the new changes. We are looking to the future and the development of new technologies, the development of online business and a whole range of other projects that we believe will be crucial in the future for market survival and overcoming the crisis in general.
What has been of immense importance to us is the availability of products for business partners and large customers whose business is directly dependent on us – not only car repairers who have continued to work, but also hundreds of carriers and public service providers who need car parts for regular operations and accessibility to citizens.
The attitude of our employees whose solidarity and understanding have and will have a large share in our future achievements also proved to be positive together with their strong desire to further optimize the business.
9. How will all this affect the development of your supply chain and Tokić company in general?
We are confident and believe that this crisis will contribute to the introduction and accelerated development of new technologies and software based on artificial intelligence, as well as business optimization in general.
From the challenges that have befallen us in recent months, we have learned that long-term plans are no longer so crucial, but the key is a quick response and the ability to adapt to the current situation. And while Tokić as a regional leader in the sector is using innovative technologies and the highest health standards, we will do everything to maintain an uninterrupted supply chain in the future. The constant in our business is trust and responsibility to customers, partners and suppliers.